With everything that businesses have had to deal with in recent times, senior leadership teams have been placed under tremendous pressure to ‘up’ their strategic game just to keep their companies afloat – let alone enable them to thrive and grow.
Richard Sadler of Birmingham-based SMMT Industry Forum shares insights from a recent survey examining learning and development trends in manufacturing organisations and asks, ‘What are the leadership lessons?’.
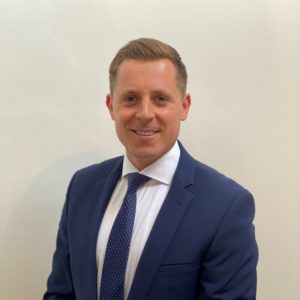
“Now is not an easy time to run a company. The COVID-19 pandemic, on the back of other rapid and tumultuous economic, technological and social developments, has created a host of complex challenges to prepare for and respond to. The stakes could not be higher. People’s health and livelihoods depend on their business leaders’ abilities to steer them safely through hazardous and unpredictable waters today, while also having the foresight to continuously reconfigure the enterprise in intelligent and innovative ways, in order to remain resilient and competitive for the future.
This stuff is hard. It requires 20:20 strategic vision, combined with the ability to inspire colleagues and customers to take action and stay the course. The leadership capabilities of C-suite teams everywhere are being stretched to the max.
They could be forgiven, then, for taking their eye off the ball when it comes to staff training. However, when we recently surveyed 141 manufacturing companies – many of them based in the industrial heartland of the Midlands – that’s not what we found.
Instead of cutting back on learning and development activities, a large number of organisations are actually increasing their investment in their key people in order to equip them with the skills and qualities needed to survive this and future storms. Almost a third (29%) of the training budget holders we spoke to saw an increase in the funds allocated to learning over the 12 months to March 2021, with a further third reporting no change. Less than a fifth (19%) experienced a budget cut. One in five companies are still investing over £500k annually in employee development.
Leadership key to survival
The single most important factor driving this training uplift seems to be the need to lead. Fifty-seven per cent of our survey respondents pointed to leadership development as a top priority this year. This makes it the most in-demand learning topic, higher even than the industry-mandated courses that are the bread and butter of the manufacturing sector. This is notable because, at Industry Forum, we usually see a far larger throughput for foundational courses aimed at shopfloor teams than those designed for senior executives, who are, of course, fewer in number.
Interestingly, the prioritisation of topics was largely the same when respondents were asked to think about the question in terms of importance to them individually and to their organisation as a whole.
All of this points to a need for leaders at every level – from team and divisional managers to chief executives – to be hyper-effective at clearly and correctly identifying and articulating the direction of travel at this critical time and bringing everyone along with them. The COVID-19 pandemic has left precious little space for inflexible or inefficient enterprises, and the difference between success and failure is the quality of leadership. Survival is not mandatory. It makes good sense, therefore, to invest in the skills and development of those with the agency and responsibility to make mission-critical decisions. And if that’s you, it can help a lot to know that you’re basing your approach on sound and proven methods.
Small and smart
It’s gratifying to see that small companies (up to 49 employees), in particular, are focussing on nurturing their talent and expanding their organisational capabilities. This section of our respondent base recorded an average annual training spend per employee of £1,128 – ten times the £101 invested by large organisations, and five times the overall average of £225.
Even considering savings bigger companies may achieve through economies of scale or conducting training in house, this points to a laudable ambition among nimble SMEs to ready themselves to grasp new opportunities and grow. We’ve worked with a number of smaller manufacturing organisations in recent months that have taken the enforced hiatus caused by COVID-19 as an opportunity to reset and recharge their strategic approach in a new direction, coming back leaner, smarter and more competitive. In turbulent times, being small and agile can be a huge advantage.
Invest wisely
At a moment when unprecedented stresses pose an existential threat to your business, you cannot afford to waste time or money on learning activities that don’t bring rapid and significant benefit.
When training senior executives, it is far more impactful – and therefore cost effective – to take a bespoke approach rather than a generic course, tailoring learning to specific individual and business requirements. At this level, time is an even more precious commodity than money, so make it count. Before embarking on any training programme, it is essential to understand where the skill gaps that really matter sit within your organisation. Then focus in with laser-like precision on the identified issues you need to tackle.
You also need to be sure that you can fully utilise your newly acquired competences. That means being prepared to follow where the training leads and change how you do things. You might need to make additional investments in areas like new technology, marketing activities or personnel, or you might have to make tough decisions about scaling back things that don’t serve your business. Everything must be on the table. After all, there’s no point training leaders and then curtailing their capacity to be impactful.
So much has changed since the start of the pandemic. Workforces and skills are transitioning to accommodate new paradigms that are still evolving, and likely to continue to change in future. The signs are that businesses across the Midlands are now starting to emerge from a difficult year into a period of renewed growth and investment. Those, like the respondents to our survey, that have invested in their senior teams, are likely to be well placed to quickly adjust to changing circumstances and climb the development curve, while the rest are still licking their wounds.”
About Richard Sadler:
Richard Sadler is Director of Business Development at SMMT Industry Forum. Richard has over 15 years of Tier One automotive manufacturing and supply chain experience. Having started his career as an Apprentice, he soon went on to hold leadership positions in Production Planning, Purchasing, Engineering and Manufacturing. Richard’s previous role was Operations Director at an Automotive Tier One, serving multiple OEMs both in the UK and overseas.
Connect with Richard on LinkedIn
FUNDING OPPORTUNITY – Midlands’ training grant opportunities
Grants of between £500 and £18,000 are now available to SMEs to upskill new and existing employees. The £12m Supplier Skills Programme (SSP) is part-funded by the European Social Fund (ESF) and managed by Birmingham City Council. It offers SMEs the opportunity to access grant funding to develop and upskill their workforce.
The programme is available to SMEs that are:
- Based within, or locating to, the “More Developed” areas of The Greater Birmingham and Solihull Local Enterprise Partnership (GBSLEP): Birmingham, Redditch, Bromsgrove, Solihull, Wyre Forest.
- Able to match fund 50% of the training costs privately.
For more information on the opportunity, please follow this link.
Please note that the promotion of this funding opportunity has been provided by SMMT Industry Forum and any such queries should be directed to enquiries@industryforum.co.uk